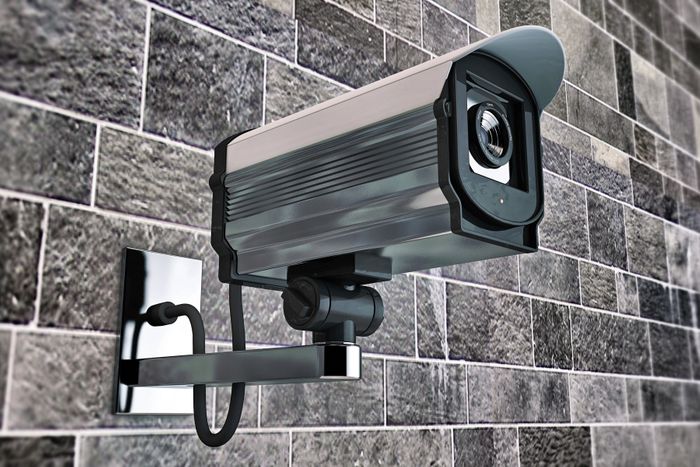
- February 8, 2021
- |security guard company, security guard services
- | 0
Alarm management is the application of human factors, engineering and systems thinking to improve the usability of a fully automated alarm system. Most often the major usability problem is that there are too many alarms annunciated in a plant upset, commonly referred to as alarm flood (similar to an interrupt storm), since it is so similar to a flood caused by excessive rainfall input with a basically fixed drainage output capacity.
However, alarm system weaknesses also include poorly designed alarm systems, improperly placed emergency alarm points, ineffective annunciation, unclear emergency alarm messages, etc. Poor alarm management is one of the biggest contributors to unplanned downtime, as well as major industrial incidents. Developing good alarm management practices is a continuous process that involves many steps over time.
The Objective of Alarm Annunciation
The objective of alarm annunciation is to alert the operator to any abnormal operating conditions. Our ultimate objective is to prevent or reduce physical and economic losses that occur in response to a hazardous or dangerous condition. For most digital control system users, losses that can result from situations that threaten environmental safety, personnel safety, equipment integrity, economy of operation, and product quality control as well as plant throughput will occur. A key factor in determining the effectiveness of the alarm response time is the speed and accuracy of the alert that an operator can identify.
The assignment of alarm trip points and alarm priorities constitutes the basic concepts of alarm management. Each individual alarm is set to alert the operator once the abnormal process condition occurs. The main issue with alarm management is that the features are static rather than dynamic. The device does not alert appropriately to changes in how it operates, or to changes in how it’s used.
Redundant Alarms are Unnecessary
When equipment, like the charge pump, compressor, and fired heater are turned off, many redundant alarms are unnecessary. These alarms are not exceptional anymore; they’re part of everyday operation. What they say doesn’t affect the outcome, and they don’t provide the operator with crucial information. During a process’ startup or shutdown, many alarms may not be useful. This is common as static alarm conditions often conflict with the required starting and stopping conditions.
In all cases of major equipment failure, start-ups, and shutdowns, the operator is required to understand which alarms signify a possible problem and how to respond to them. Delayed action due to this takes away important time when making important operating decisions and taking swift action is necessary. If the overall volume of alarms becomes too great for the operator to be able to comprehend, then the basic alarm management system has failed as a system capable of alerting the operator quickly and efficiently in the event of an alarm. In instances such as these, the operator has very little chance of avoiding a significant loss. Contact XPressGuards today and we’ll help your manage you alarm system in the most efficient way possible.